DMLS (Direct Metal Laser Sintering) parts require heat treatment after building to relieve thermal stresses induced in the process. These stresses cause parts to warp and curl if they are removed from the building platform without heat treatment. The following picture is an example of how the thermal stresses can affect parts without heat treatment.

During the heat treating process, the parts and the building platforms oxidize if left in an untreated atmosphere. As argon is pumped into the furnace, being a heavier gas, it will slowly displace the ambient air up and out of the furnace to prevent oxidation.
his is the SolidWorks model of the planned diffuser Spencer Thompson and I developed. Argon will be pumped into the furnace via a tube connecting with the diffuser at the vertical tube. Platforms with parts still attached will rest on top of the squares placed around the ring. There are holes periodically spaced throughout the ring to release the argon evenly. These holes also vary in size, from ¼ – 1 mm in ¼ mm increments. These holes will give us an insight to the capabilities of the EOS machine to produce through holes in parts.

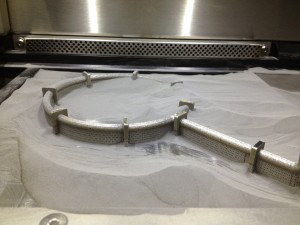
The diffuser ring was made out of cobalt chromium on our EOS M280 DMLS machine. This build was approximately 10 hours. The pictures above show the build in progress and the completed part during the removal process.
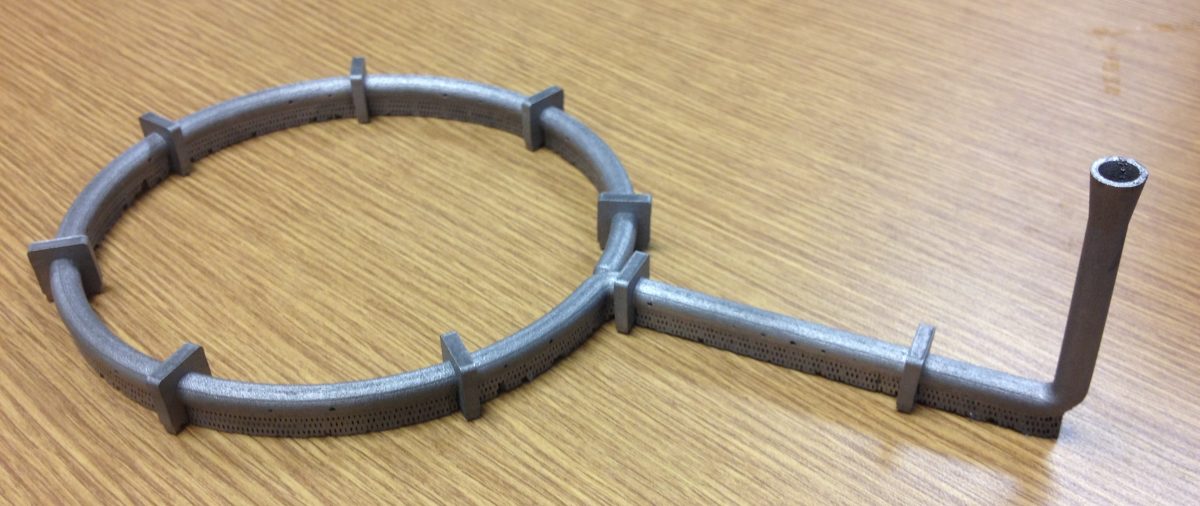